CASE STUDY
St. Luke's University Health Network
Read how they used actionable insights from CensiTrac and CensisAI2 to unlock a 20% increase in productivity.
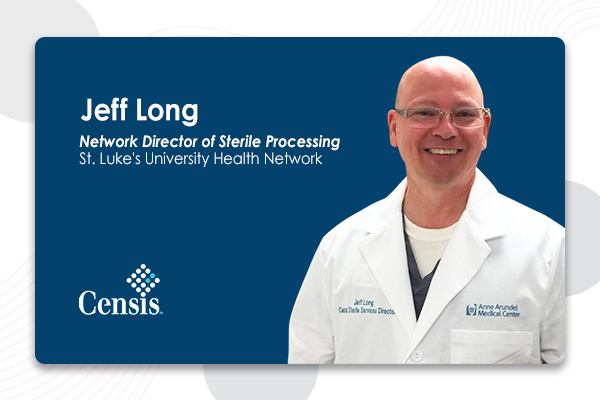
Pennsylvania
12 Campuses
17,000 Employees
St. Luke’s University Health Network (SLUHN) is a regional, non-profit network of more than 17,000 employees who provide services at 12 campuses and more than 300 outpatient sites. With staff based in numerous locations, SLUHN was looking for more ways to improve communication and increase visibility into sterilization processes across sites.
Jeffrey Long, Network Director Sterile Processing, describes how in the past, he relied on Excel to input data and generate reports. “I was spending three to four days a week getting data just so I could do a report once a week.”
In their search for better way, Jeffrey and his team turned to CensisAI2 Productivity. Now, the team is able to see the data they need in seconds. For example, Jeffrey describes how the productivity platform provides visibility into the number of trays sterilized by specific staff members each day.
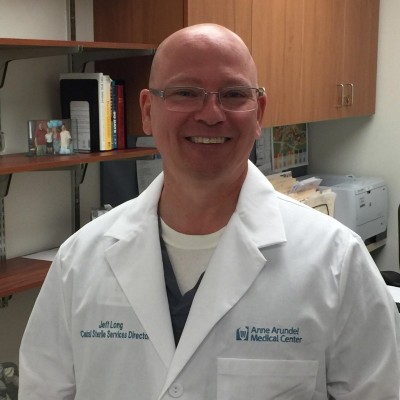
"Armed with the data we were able to make changes that enabled our sites to process 5,000 more trays a month with the same staff, a 20% increase in throughput that went straight to the bottom line."
Jeffrey Long
Network Director Sterile ProcessingCensisAI2 Productivity also provided vital visibility and comparisons of tech-to-tech, shift-to-shift, and site-to-site data. With this data available at their fingertips, the overall efficiency and performance of SPDs across all their network sites improved.
Jeffrey described how CensisAI2 Productivity enabled him and his team to see that one site was performing 42% of sterilization work for the entire network. The data also showed that the particular site took an average of 10 seconds longer to sterilize and arrange trays.
Knowing this, Jeffrey and his team were able to use data from CensisAI2 Productivity to more accurately predict the number of full-time employees (FTEs) needed to support their caseload. Data showed that allocating FTEs based on the number of trays processed worked at some facilities but not at those with more complex or a higher number of instruments in the trays. As a result, they were understaffed and running overtime to keep up with the workload. Using CensisAI2 Productivity, Jeffrey and his team were able to justify the need for an additional four technicians to reduce burnout and turnover as well as reduce costs.
Armed with this data, SLUHN has been able to make valuable improvements across their hospital network — improving SPD throughput and getting a rapid ROI for the CensisAI2 Productivity platform.
“Knowing what you need and what you’re looking for can be really difficult with standard reports. CensisAI2 showcases data really clearly which allows users to easily find information and drill down into it. Without this data, it would be difficult to make decisions."
Jeffrey Long
Network Director Sterile Processing
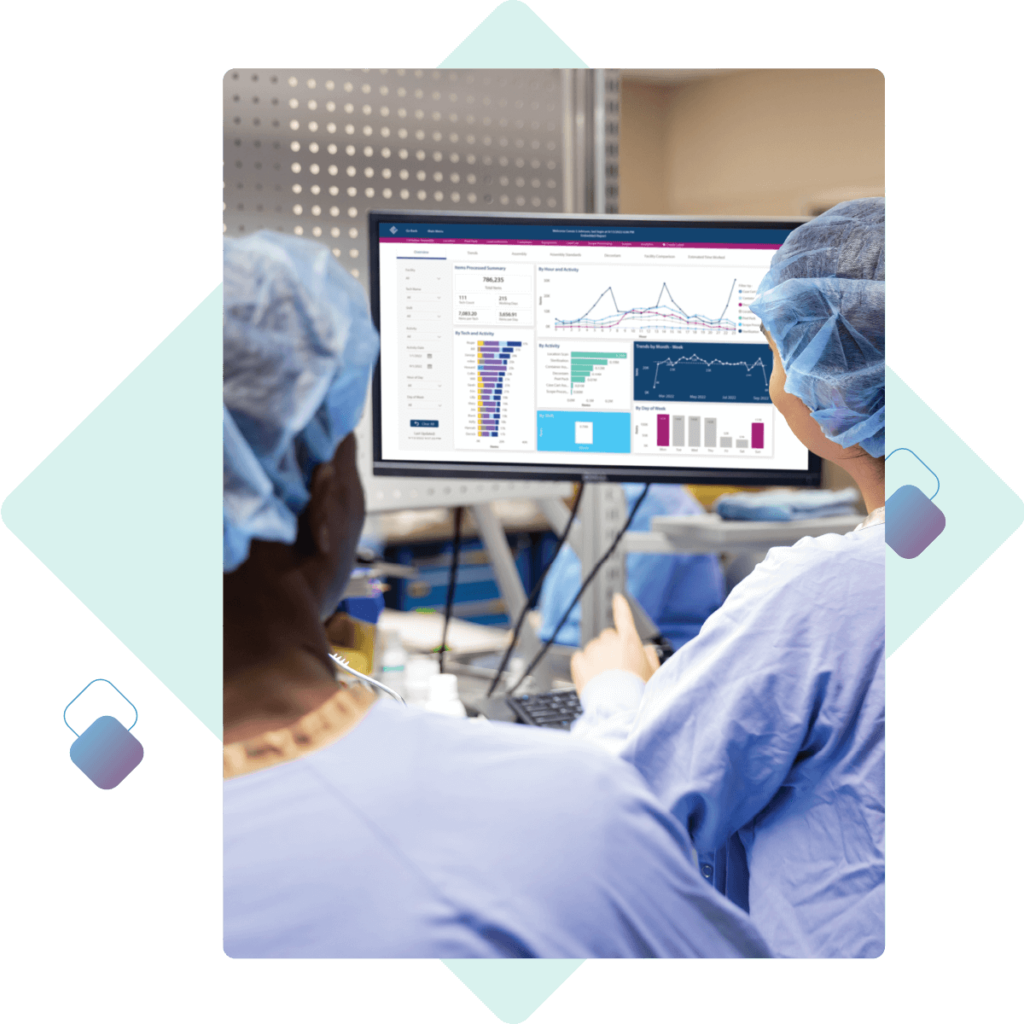
The Insights You Need to Increase Throughput
Whether you're looking to increase throughput, streamline reporting, improve communication, or reduce errors, CensisAI2 enables teams to achieve each of these goals by unlocking the actionable data insights you need, but haven’t been able to easily access — until now.
More Customer Stories
Williamson Medical Center
Read how Cody used actionable insights from CensiTrac and CensisAI2 to optimize department productivity.
St. Francis Hospital
Read how James used actionable insights from CensiTrac and CensisAI2 to strengthen relationships with other departments.